Two Characteristics Hold Key to Nail Quality
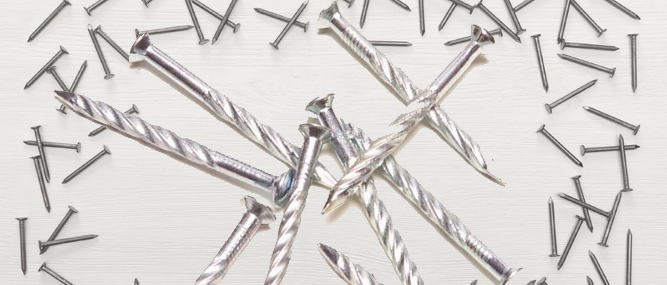
Expert explains the science behind picking the right nail for your application.
Pallet companies can get a leg up on their competitors by ensuring they are using the best fastener for assembling wooden pallets. They will be able to distinguish themselves from the competition by choosing a nail that improves pallet quality, does a better job of protecting a customer’s product, and reduces the per-trip cost of the pallet.
“Product differentiation is a standard marketing technique, and the fastening system is an inexpensive way to dramatically separate your product from the competition,” said Marshall “Mark” White, former head of the Virginia Tech Center for Packaging and Unit Load Design and the university’s William H. Sardo Jr. Pallet and Container Research Laboratory.
Most damage sustained by pallets occurs in joints, by the nail head popping above the deck board or complete separation of the joint. The quality of the fastener, however, can impact the frequency and level of damage.
“Nails vary tremendously in quality,” noted Mark, who continues to work on a part-time basis at Virginia Tech and also has his own consulting business, White & Company.
“The range of fastener quality available for pallet assembly represents a 10-fold difference in resistance to rough handling and pallet life,” he added.
In addition, for the pallet manufacturer, the cost of fasteners – independent of fastener quality – is relatively small.
The two most common types of nails used in assembling pallets are helically-threaded or drive-screw nails and annularly threaded or ring shanked nails. Of the two, helically-threaded or drive-screw nails are most frequently used in pallet assembly.
However, annular nails are just as good as helical nails of similar thread quality, noted White. “The annular nail has better withdrawal resistance, so we recommend this thread for low density hardwoods and most softwoods. However, the helical nail of the same gauge has better bending resistance, so it is recommended for medium and high-density hardwoods.”
There are a number of characteristics that impact nail quality, including wire diameter, thread characteristics, and other factors. However, it’s informative to look at how pallet joints fail, and specific nail characteristics that impact failure.
Pallet joints fail two ways. The nail head may pull through the deck board (nail head pull-through), or the nail shank may pull out of the stringer or block (nail shank withdrawal failure). Nail head pull-through typically is caused by the bending of the nail and the resulting splitting of the deck board.
Of all the characteristics that impact the quality of helically-threaded nails, the two most significant are the difference between wire diameter and thread crest diameter, and the bending stiffness of the nail, explained White.
The difference between the thread crest diameter and wire diameter, which is directly related to the thread depth and the angle of the thread, are the characteristics that most affect nail shank withdrawal failure. A general rule to remember, the greater the difference between nail wire and thread diameter, the greater the quality of the nail and its resistance to shank withdrawal. In fact, thread crest diameter is one of the most critical nail characteristics that affects withdrawal resistance.
If the difference between nail thread and wire diameter is more than 0.020 inches, relative nail quality is excellent. When the difference drops to 0.016 to 0.020 inches, relative nail quality drops to good. A difference of 0.012 to 0.015 inches is marginal, and less than 0.010 inches is considered poor.
For helically threaded nails, thread angle also is a key characteristic impacting withdrawal resistance. Thread angles of 67 to 68 degrees are typical. Thread angles of 77 degrees or greater are typically called ‘lazy’ threads and are of poor performance.
Nail head pull-through resistance is a function of deck board species and thickness and also the diameter and strength of the nail head. However, according to White, most nails today are over-designed as far as head pull-through resistance. In fact, head pull-through resistance typically is greater than shank withdrawal resistance.
Most nail head pull-through failure is associated with bending of the nail because of impacts on leading edge deck boards. When the nail bends, it tends to cleave or split the wood, and the deck board will pull off at that point, leaving the nail in the stringer. The more the nail bends, the more likely this type of failure will occur.
One measure of bending resistance in nails is known as the MIBANT angle, which is measured by a MIBANT (Morgan Impact Bend Angle Nail Tester) testing device. The MIBANT angle of most pallet nails ranges from 8 to 46, with the lower the angle, the greater the quality of the nail.
A MIBANT angle of 8-24 degrees is considered excellent for relative fastener quality; 25-35 degrees is good, and 37-46 is acceptable. A nail with a MIBANT angle greater than 60 degrees is much lower quality and only acceptable for clinch nailing for deck board and stringer board joints in block-style pallets.
“We’ve been around and around and around,” said White, referring to improvements in fasteners and studying the relationships between nail performance and pallet performance, and factors like nail thread characteristics and steel chemistry and their impact on pallet performance. “We know how to improve the quality of the nail.”
There have been various attempts over the years to improve fasteners for wood pallets, commented White. Some were attempts to improve nail performance, such as the annular over helical, double- threaded nail, while others were aimed at efficiency by using less metal per nail, such as the so-called “Star” nail.
So-called “nail screws” have excellent withdrawal resistance. They insert as screws, though, and therefore are slow to insert. “Generally, they are brittle because the head has to be hard to connect to the turning head of the driver,” said White. “They can break on impact. I believe the jury is still out on acceptance of screws in pallets.”
Screws are frequently used in assembling crates and containers, stated White, as well as staples. “We see more screw usage primarily because a crate isn’t exposed to the same kind of stresses as a pallet deck board,” and the brittleness of a screw is much less problematic.
The Virginia Tech lab can provide a Fastener Quality Analysis form to collect information from suppliers to help determine nail quality. If a vendor or supplier is not willing to provide the information, the lab will test samples for a fee. Pallet manufacturers also can obtain a set of calipers and a MIBANT testing device to assess the quality of their nails. The lab also can test pallets assembled with different fasteners to determine relative resistance to rough handling due to fastener selection.
NEXT:2019 Steel Price Forecast